Корпоративен университет
TPM - Ефективна поддръжка на оборудване
TRM (Тотално управление на производство) е система от планирани действия на работниците, инженери, техници, като екип, насочени към максимизиране на ефективността на неговото оборудване чрез превантивна поддръжка през целия жизнен цикъл.
TRM - това е инструмент за подобряване на цялостното представяне, предприятието хардуер като единна система.
TRM - това е работа в екип, своеобразно продължение на системата 5S.
Без TPM е невъзможно да се въведе някакъв вграден в качеството, нито на системата "точно навреме" и неговия инструмент Kanban или Poka-игото устройства (защита грешка) се обезсмисля SMED (бърза смяна).
Освен това, в някои случаи, TPM може да бъде най-важният инструмент на "постно производство". Например, ако ви се произвеждат продукти на автоматизирано оборудване. И в продължение на няколко местни предприятия, докато, уви, това е не само важна, но също така е единственият. И въвеждането на всички останали елементи на "постно производство" Тогава тя преминава през развитието и разпространението на TPM.
Целта на TPM - е създаването на компанията, която непрекъснато се стреми да ограничи и да се подобри ефективността на интегрираното производство система.
Средство към целта е създаването на механизъм, който обхваща преки работни места, е насочена към предотвратяване на всички видове загуби ( "нулево ниво на злополуките", "нула щети", "нула брак") по време на целия жизнен цикъл на производството.
За да се постигне целта включва всички отдели: инженерство, бизнес, мениджмънт, и преди всичко, продуктивни.
В постигане на целта за всички служители, участващи - от върховния лидер на "първа линия" на работника или служителя.
Желанието да се постигне "нулеви загуби" се изпълнява в рамките на йерархично свързани малки групи, в които са обединени всички служители.
Какво може да TPM компанията?
Целта на изпълнението на TPM, както бе споменато по-горе, - за да се постигне максимална ефективност и интегриран системи за производство. С други думи, за да се получи възможно най-добрия резултат в производството otnosheniiobema (производство - P), качеството на продуктите (Quality - Q), цената (цена - C), време за доставки (за доставка - D), работни места за сигурност (безопасност - S) и инициатива на персонала (Moral - М) с минимално използване на човешки, материални и финансови ресурси.
Таблица 1 показва средните данни за няколко японски компании - победителите награда TPM, характеризиращи както осезаеми резултати, които са постигнати, както и на нематериалното ефекта от въвеждането на тази система.
Преди появата на TPM се е смятало, че в природата на растението е "развъдник" на трите "К" (с това писмо в японския език започва с думите - "мръсотия", "трудни условия", "опасност").
Което елиминира загубата: Времето, прекарано в отстраняване на хардуер.
Основната част на TPM е сътрудничеството между операторите и сервизи, с активното участие на ръководството в областта на ранното откриване и предотвратяване на проблеми и контрол върху състоянието на оборудването.
1. Необходимо е да се разработи прост език, разбираем за операторите и не изисква специална подготовка за тях и, в същото време, достатъчно информативно за сервизи (например стандартизирани качествени описания несвойствени шумове на двигателя, и така. Г.).
3. Важна част от TPM е систематичен документиране на данни от общата производителност на оборудването. Ако тези данни се поддържат в продължение на дълъг период от време, те често показват спад в представянето си много преди основните причини за този спад ще доведе до пълна производствена стоп. Логично е да направи процеса на документиране на тези данни като прост и тежки. В повечето случаи е достатъчно да се разгледа само 3 съотношение:
а) наличието, изпълнението и добива продукт, определя, както следва:
Наличност = теоретична времето за работа / Налично време като цяло;
Изпълнение = действителния капацитет / теоретичен капацитет;
добив на продукта = добив на продукти от първия опит / Действителен производителността.
TPM включва подобряване на ефективността на производствената система чрез премахване на всички загуби за по-ефективно като човешки труд и използването на оборудване, енергия, суровини, материали и инструменти. Обикновено производствени индустрии отделят 16 загуба видове. Тази цифра може да бъде удължен за всеки отделен предприятие.
В съответствие с този подход за оценка на ефективността на системата за производство не е местните показатели се използват в TPM, като коефициента на натоварване на оборудването, както и степента на общата ефективност, отразяващи всички видове загуби. Връзката между общата ефективност на оборудването и основни видове загуби, както и процедурата за изчисляване на коефициента на общата ефективност на оборудването.
Според концепцията на TPM, е основна пречка пред ефективното използване на оборудването се състои от два вида повреди: причинява изключване на оборудване и да доведе до отклонение от нормалния ход на работа и следователно водещи до брак или друга загуба.
Счупване - на "върхът на айсберга", която израства от скритите дефекти. Като прах, мръсотия частици стърчат материал износване, разхлабване, реакция, корозия, деформации, пукнатини, вибрации и др ..
Скрити дефекти се натрупват и подсилват взаимно, в резултат на което настъпва счупване.
Практиката на TPM се разграничат две групи причини за скрити дефекти не е дадено необходимото внимание.
Първата се корени в човешката психология. Скрити дефекти не се възприема от окото, те не обръщат внимание, те нямаше да съществува, и следователно те не знаят, че те са причината за провала.
Втората група причини е свързана с оборудването си и да създаде свои оперативни процедури. По-специално, не се предприемат мерки за отстраняване на явления, причиняващи латентни дефекти (прах, мръсотия, т. П.). Оборудването е често проектирана така, че да не могат да бъдат открити всички скрити дефекти, защото всичко се затваря капаците, или затруднено поради затруднения достъп до чистка, смазване, затягането на болтовете.
Външният вид на скрити дефекти се влошава състоянието на оборудването, което води до отклонение от нормалното си състояние. Ето защо, TPM е разработила система за идентифициране на скрити дефекти и привеждане на оборудването към нормалното състояние.
"Нулева счупвания" TPM се постига чрез постепенно, систематично и последователно прилагане на петте групи дейности:
- създаване на основните условия за нормална работа на оборудването;
- съответствие с условията на работа на оборудването;
- възстановяване на нормалното износване;
- премахване на структурна (причинено от проекта) липса на оборудване;
- подобряване на уменията на операторите, ремонт и поддръжка, дизайн инженери.
Трябва да се подчертае още веднъж, че при изпълнението на тези дейности, включени абсолютно всички подразделения на фирмата.
ОБЩА оборудване Висока производителност в съответствие с концепцията за TPM вече определени на етапа на проектиране. Той първоначално е трябвало да бъде надежден и безопасен, лесен за използване и поддръжка, икономична консумация на ресурси.
Централният концепцията за TPM - разходите за целия жизнен цикъл - Life Cycle Cost (LCC) - включва разходите за оборудване и разходите за нейното функциониране през целия експлоатационен живот. Изборът на оборудване и неговите методи на работа се извършва така, че да се сведе до минимум разходите за оборудване и разходите за нейното функциониране през целия експлоатационен живот.
В TPM, като, наистина, и във всичко, което се отнася до качеството, това е от съществено значение не само в резултат на въвеждането на тази система, но също така и в процеса на въвеждането му. Освен това, ако разполагането се организира правилно, и очакваните ползи почти със сигурност няма да бъдат получени.
Това обяснява повишеното внимание се отделя на развитието на TPM в екшън сцените и организационна структура за насърчаване на този наистина ефективна система.
При извършване на основни ремонти и подходящи грижи, дори и за съществуващите производствени мощности могат да увеличат своята функционалност и точност при 20-30%. С други думи, основната система е ефективна, за да работи с оборудването, за да се установи кой трябва да започне веднага. И само за наличието и степента на развитие на една такава система зависи от това дали компанията ще бъде в състояние да копая всички разпоредби на тяхното съществуващо оборудване и осигуряването на нови грешки и да се избегне загуби, които неизбежно възникват при липсата на такава система.
Въпреки факта, че на базата на TPM са като цяло проста идея, нейното развитие изисква много усилия и време - от 3 до 10 години, тъй като включва фундаментална промяна във философията, така и психологията на отделния работник и целия набор от отношения между служители на компанията , Въпреки това, както показва опитът на компании, които са внедрили тази система, резултатите са точно такива промени и сега възлизат на един от основно конкурентно предимство на света
трудности при изпълнението
- Тази неспособност да се види целия процес с пускането на ограничаващите фактори в нея.
- то е присъщо на счетоводната система на желанието за местно оптимизиране на някои операции, понякога за сметка на увеличаване на капацитета на целия поток, и работниците заплатите ефективност.
- Това нежелание да делегира управлението на власт на тези, които най-добре знаят техника, която работи, и т.н.
В обхвата на приоритетната заявка:
В съвременните условия, когато не само производството, но също и за офис, пълен с сложна апаратура, приложимостта на TPM е в близост до универсален, въпреки че TPM все още не харесва 5C, което е предпоставка за използването на всички други методи за стегнато производство. Според експерти, повечето от използването на TPM може да доведе до производството на процеса.
Предишни приложения: Икономически TPM ефект също така лесно да се смесва с други икономически ефект Lean инструменти, макар и като цяло по-рядко, отколкото TRM 5C. По-специално, значителния напредък, постигнат в прилагането на TPM производителите на алуминий, като световен производител №1 Alcoa и Русал лидер на българския пазар.
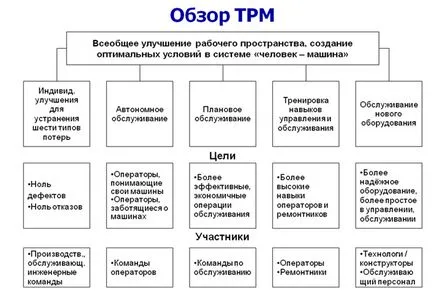