Каталитично реформиране - studopediya
Състав на бензинови фракции причинява най-ниско октан първичен бензин, обикновено не повече от 50 точки. Освен първичен бензин като суровина за каталитичен риформинг използване бензини на вторични процеси - термичен крекинг и коксуване след дълбоко хидротретиране и хидрокрекинг. Първичен добив бензин е относително ниска (около 15-20% от маслото). Също така част от бензин използва за други цели (суров пиролиза, производство на водород, получаването на разтворители и т.н.). Следователно, общото количество изходна суровина се преработват в каталитичен риформинг, обикновено не надвишава потенциал съдържанието на бензинови фракции в петролен етер.
Реакцията на мишена са ароматен въглеводород формация в процесите на каталитичен риформинг чрез:
1) дехидрогенирането на шест-членни циклоалкани
2) dehydroisomerization циклопентани
3) дехидроциклизация (С5- или С6-дехидроциклизация) парафинови въглеводороди

Успоредно с поток процес и нежелани реакции хидрокрекинг за производство на двете ниски и високи въглеводороди молекулно тегло, както и кондензационни продукти - на кокс се отлагат върху повърхността на катализатора.
Най-важното реформиране реакция, водеща до образуването на ароматни съединения от парафини и нафтени, са с абсорбция на топлина, на изомеризация реакцията на нафтени и парафини имат термичен ефект близо до нула, и хидрокрекинг реакции са екзотермични.
Превръщането на нафтенови и парафинови въглеводороди до ароматни - обратими реакции, наблюдавани с увеличение на обема и абсорбция на топлина. Следователно, съгласно правило Le Шателие на дълбочината равновесие на ароматизиране увеличава с повишаване на температурата и намаляване на парциалното налягане на водород. Въпреки това, промишлените процеси реформиране принудително провеждат или при по-високи налягания, за да потискат реакции за образуване на кокс (по този начин понижаване на дълбочина ароматизиране на равновесие компенсира повишаването на температурата) или непрекъснато регенериране на катализатора при ниски налягания.
Процесът на каталитичен реформинг се извършва на бифункционални катализатори, комбиниращи киселинни и хидрогениране-дехидрогениране функция. Хидрогениране и дехидрогениране реакции се провеждат на платина или платина рений насърчава от добавки, иридий, калай, галий, германий и др фино диспергирана върху подложката. Киселинната функция в търговски реформинг катализатори извършва носител, който се използва като алуминиев оксид. За функциите на амплификация и регулиране киселинен носител в състава на катализатора се прилага халоген: флуор или хлор.
Качеството на суровина реформиране определя фракционна и химичен състав на бензин. Фракционен състав на суровината е избран в зависимост от целта на процеса. Ако процесът се провежда с цел получаване на отделни ароматни въглеводороди, за производството на бензен, толуен и ксилен се използват съответно фракции, съдържащи въглеводороди С6 (62-85 ° С), C7 (85-105 ° С) и С8 (105-140 ° С) , Ако реформирането се провежда за получаване на високооктанов бензин, суровината е обикновено част от 85-180 ° С, съответстваща въглеводороди С7-С10.
Тъй като процесът на реформиране силно ендотермична, тя се провежда в каскада от три или четири реактора с междинно съединение се нагрява суровина. В първия реактор в хода на суров простира обикновено протича с висока степен на реакция е силно ендотермична дехидрогениране на нафтени. В последния реактор, ендотермични реакции възникват предимно дехидроциклизация и достатъчно силна екзотермична реакция, хидрокрекинг на парафини. Поради това, в първия реактор имат най-висока (30-50 ° С) и последната малката разлика (градиент) между температурата на входа на реактора и изхода от тях. Високо температурен градиент в главата реформиране реактори може да се намали, ако дълбочината на стесняване срещащи се в тях ароматизиране реакции. Това може да бъде постигнато в даден режим температура само намалява времето за контакт на храна с катализатора, т.е. обем на катализатор в него. В тази връзка, в промишлени инсталации реформинг глава реактор има най-малкото количество от катализатор и опашката - по-голям. За обем катализатор trehreaktornogo разпределение единица етапите на 1: 2: 4 до 1: 3: 7 (в зависимост от химическия състав на суровината и желания процеса на дестинация), и за chetyrehreaktornogo може да бъде, например, 1: 1,5: 2 5: 5.
Тъй като компонентите на цялостния процес на реформинг реакции са неравни активиране енергии - максимални реакции хидрокрекинг (117-220 кДж / мол) и минимална за реакциите на ароматизация (92-158 кДж / мола), след това температурата се повишава до голяма степен на хидрокрекинг реакции се ускоряват от ароматизиране реакция. Затова обикновено се поддържа при нарастващ температурен режим каскада от реактори, което намалява ролята на реакциите на хидрокрекинг в горната част на реактора, като по този начин да се повиши селективността на процеса и увеличаване на добива на реформат. Температурата на входа на реформинг реактор е разположен в началото на реакционната цикъл до ниво, което осигурява предварително определено качество реформат - брой октан или концентрация на ароматни въглеводороди. Обикновено първоначалната температура в интервала 480-500 ° С и само при работа в тежки условия е 510 ° С Както коксуване и загуба на активност на температурата на катализатор на входа на реактора се увеличава постепенно, като се поддържа постоянно качество на catalysate, при средна стойност за скоростта на повишаване на температурата на живота на цикъл между 0,5-2,0 ° С на месец. Максималната температура на нагряване на суровината въвеждане на последния реактор с неподвижен слой катализатор достигне 535 ° С, и в настройките с непрекъснати реактори регенериране - 543 ° С
Налягане - главен, заедно с настройките на температурата корекция, която има значително влияние върху добива и качеството на реформинг. С други параметри идентични с понижаване на водородни частични повишаване на налягането като термодинамично и кинетично възможно дълбочина и ароматизиращи материали, най-важното, повишава селективността на превръщането на парафинови въглеводороди, тъй като падът на налягането благоприятства потока на реакциите на ароматизиране и инхибира хидрокрекинг реакции. Въпреки това, при по-ниско налягане процес увеличава скоростта на катализатор деактивиране поради коксуване. При налягане 3-4 МРа образуване на кокс е потисната до такава степен, че преобразувателя с неподвижен слой на катализатора може да се задейства без регенериране почти 1 година. Използването на двустранна и полиметални катализатори позволява да се извърши процесът на 1.5-2.0 МРа без регенерация катализатор в рамките на 1 година.
Многообразието hydrogenous циркулация на газ. Този параметър се определя като съотношението между обема на водород-съдържащ рециркулационен газ (HBG), редуцира до стандартни условия, на обема на изходна суровина, преминаваща през реактора за единица време. Като се има предвид, че концентрацията на циркулиращия ИЗМИВАНЕ водород варира в широки граници - 65-90% об. и молекулното тегло на суровината зависи от фракционните и химически състав, за предпочитане като се използва моларно съотношение водород. Суровини (понякога мола водород на мол суровина въглерод). С увеличаване на моларното съотношение на водород. Суровини намален размер на деактивиране на реформинг катализатори, и по този начин удължава IPSO практика. Избирането на тази опция ще доведе със стабилността на катализатора, качеството на суровини и продукти, процеси и твърдост на предварително определена продължителност пълноправно факто. Когато се използва в инсталации с неподвижен катализатор полиметални катализатори моларното съотношение на водород. Raw равно на 5. 6 осигурява води по продължителност на цикъла до 12 месеца. Тъй като най-високата скорост на катализатор деактивиране обикновено се случва в последния реактор поради високото съдържание в реакционната среда от ароматни въглеводороди и режим риформинг трудно. Подравняване на катализатора чрез коксуващи реактори от реформинг единици в някои модели в последната част на реактора допълнително служи измиване.
обемен храна влияе на процеса на реформиране като параметър, времето на обратен контакт храна с катализатора. В съответствие със законите на химически кинетика с увеличаване обемна скорост (т.е., намаляване на времето за контакт) се редуцира реакции суров дълбочина ароматизиране и хидрокрекинг реакции много повече парафини. В този намалява добив хидрокрекинг продукти - леки въглеводородни газове и кокс върху катализатора. Ароматни въглеводороди са оформени главно поради нафтен дехидрогениране реакции се провеждат значително по-бързо, отколкото други. В резултат на увеличаване резултати обемна скорост фуражни:
- намаление на добива измиване висока концентрация водород;
- подобряване на селективността на процеса и удължаване на продължителността на IPSO практика.
От друга страна, с намаляване на обемната скорост на фураж се намалява реформиране единици производителност на суровина. Оптималната стойност на WHSV се задава като се има предвид качеството на суровината реформинг стабилност катализатор и твърдост.
Каталитичен риформинг с неподвижен слой на катализатора
Инсталации от този тип понастоящем са най-широко между процесите на каталитичен риформинг на бензин. Те са предназначени за продължителна работа без регенерация за 1 година или повече. Оксидативен регенериране на катализатора се извършва едновременно във всички реактори. Общата продължителност на времето за престой инсталации с реактор с неподвижен слой е 20-40 дни в годината, включително и на цикъла и ремонта регенерация. растителна суровина е предварително дълбоко хидротретиране на сяра, азот и други съединения, както в случая на рафиниране бензинови вторични процеси - хидриране на ненаситени въглеводороди.
всички видове каталитичен риформинг инсталации включват следните блокове: пречистване на хидротретиране суровина от водород-съдържащ газ, в реактора, отделяне на газ и стабилизиране catalysate.
Монтаж платформинг диаграма схематично поток (без блок хидротретиране суровина) с катализатор с неподвижен слой е показано на фиг.
Монтаж схематична поточна диаграма
каталитичен риформинг с неподвижен слой на катализатора
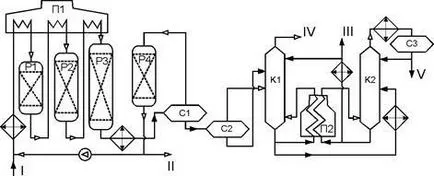
I - Хидрогенирано суровина; II - измиване; III - стабилен catalysate;
IV - сух газ; V - горната фракция
И изсушаване хидротретиран суровина се смесва с циркулиращ измиване, предварително нагрята в топлообменника, а след това в секцията пещ Р-1 и се подава към реактора R-1. Заводът има три или четири адиабатно реактор и съответен брой секции многокамерни пещ P-1 за междинните нагряване на реакционната смес. На изхода на последния реактор се охлажда в топлообменник и хладилник до 20-40 ° С и се подава към сепаратор за високо налягане S-1 да се отдели от циркулиращия ИЗМИВАНЕ catalysate. ИЗМИВАНЕ част след сушене зеолита в адсорбер П-4 се подава към приемането на компресора на циркулация, и излишъкът от изхода на временния блок бензин хидроочистка и се предава към други потребители на водород. Нестабилна catalysate на С-1 се подава към сепаратор ниско налягане S-2. където леки въглеводороди се отделят от нея. Отделените в сепаратор S-2 газ и течни фази се подават към фракциониране абсорбер К-1. Абсорбиращи е стабилен catalysate (бензин). В долната част на абсорбера се загрява от поток горещ пещ чрез Р-2. В абсорбера при налягане от 1.4 МРа и температура под 165 и над 40 ° С отделя сух газ. Нестабилна catalysate изведен от дъното на К-1. След нагряване в топлообменника се подава към колона К-2 стабилизиране. Загрява се в долната част на К-2 и хранени циркулация фурна загрява до 1 част п-стабилен кондензат. Фракцията над след стабилизиране кондензация и охлаждане подава към приемника-3. от частично рециклирана към K-2 за напояване и излишък изхода с инсталация. Част catalyzate стабилен след охлаждане в топлообменника се подава към абсорбиращата фракциониране К-1. и остатъка от своя излишък извежда от растението.