Термична обработка на пружини
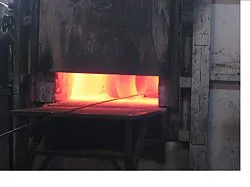
Еднакво важно за пружините и метални пружини и обработва свойства - ниска тенденция за растежа зърно и decarburization време на топлинната обработка. дълбоко закаляване. ниска критична скорост на закаляване. ниска чувствителност към нрав крехкост.
Качеството на извора се отрази на състоянието на повърхността на пръчките. проводници и ленти. Наличието на външните дефекти (пукнатини. Залези. Плен. Косата. Черупки. Грапавини. Потиснато мащаб и др.) И обезвъглеродяват слой намалява еластичните свойства на метала и циклични. Следователно, външните повърхностни дефекти на пръти и ленти трябва да бъдат отстранени чрез смилане или шлифоване. и дълбочината на обезвъглеродяват слой не трябва да надвишава определени стандарти. ГОСТ инсталиран на пролетно-стомана пролетта.
За производството на пружини използвани въглерод и легирана стомана. и за инструменти - цветни метални сплави. главно берилий бронз. Изворите са изработени от само легирана стомана.
И пролетта ресор е подсилена по следните начини:
Вместо патентоването икономически по-изгодно да се използва метод за нормализиране на закаляване стомана. Този метод. разработена в Горки автомобилен завод. Това е, както следва. Тел. пръти. ленти от стомана 45. 65g. 50HG подлага на нормализация. и след това студено изтегляне или пластична деформация от подвижния при деформация на 40-60%. От получения полуфабрикати раната продукт. произведен чрез щамповане или режеща пластина и винтови пружини. пружинен лист. което се подлага на нагряване при 280-300 ° С в продължение на 20-40 минути.
При нагряване, има процеси на щам стареене. причинява втвърдяване. граница на умора по този начин по-горе. отколкото след закаляване и отвръщане. Например. граница умора на стоманената плоча вода 65g след щам стареене б = 96 кгс / mm 2 (960 MN / m2) и след втвърдяване и темпериране б = 77 кгс / mm 2 (770 MN / m2). Предимството на този метод е фактът. при условие, че размерът и формата на еластични елементи. което е особено важно за тънки листови ресори. силно деформирани при закаляване. За да се премахне изкълчване на пружините трябва да се използва със специални печати почивка.
Втвърдяване чрез охлаждане, последвано от темпериране.
За производството на пружини. втвърдяващ чрез топлинна обработка (закаляване и отвръщане) се използва въглен (65. 75) и легиран (60S2A. 50HFA. 60S2N2A и др.) стомана. пролетта - легирани стомани само. за извори. в агресивни среди, - неръждаема стомана 30X13. 40X13. 12X18H10T и сътр.
Въглеродна стомана, поради ниската им закаляване се използва за производство на пружини от диаметъра на проводника до 6 мм. Предимство на стоманата на силиций в сравнение с въглерод - тя увеличава закаляване и висока якост и пластичност. Недостатък на тази стомана е повишена склонност към образуване на повърхностни дефекти по време на гореща обработка. decarburization и графитизиране. В резултат на decarburization на външната повърхност на пружини е намалена значително удължено тяхната устойчивост на корозия. Следователно, отопление на пружини трябва да се извършва със защита от или decarburization (за премахване на вредното влияние на decarbonized слой), за да ги излага на топлинната обработка след пясъкоструйна обработка.
Широкото използване за производство на пружини на моторни превозни средства и пружини на железопътни превозни средства имат 55S2 силициеви стомани (А) и 60S2 (А). Steel 60S2 (A) се използва и за производство на пружини. функционират при температури до 250 ° С 70SZA стомана има високи механични свойства. но склонни към Графитизация.
Манганова стомана (65g) в сравнение с силиций стомана има определени характеристики. които включват получаване на по-малко грапава повърхност в гореща обработка. страхотно за закаляване и по-малко склонни да decarburization. Недостатъци на манганова стомана се увеличават чувствителността към прегряване. образуване на закаляване пукнатини. склонност да се темперира крехкост; стоманата, използвана за механизми пружини и машини.
Подробности за 55GS стоманени профили до 25 мм имат закаляване. и поради това се използва за производство на пружини дебелина до 10 мм. винтови пружини с диаметър прът и буферни пружини 25 мм; тази стомана malosklonna да decarburization и нрав крехкост.
Chrome манганова стомана (50HG (A)) има дълбоко закаляване. висока якост и относително ниска чувствителност към прегряване; се използва за производство на пружини на голямо напречно сечение; стомана гаси в масло и; недостатък на тази стомана е тенденцията да се темперира крехкост.
Частично добавка към ванадий хром стомана има положителен ефект върху структурата и еластичността. и намалява неговата склонност да прегрява. при което топлинна обработка е значително улеснено; обаче хром (50HFA) и hromomargantsevanadievaya (50HGFA) да стане и закалени в масло и malosklonny за растежа на зърно. Използва се за производство на тези стоманени пружини особено критични приложения. както и изворите на автомобили.
60S2HFA стомана. 65S2VA 60S2N2A и се използва за големи натоварвания извори. Подробности за тези стомани malosklonny за растежа на зърно и калцинирана в секции до 50 мм. Особено високи качества има nikelkremnistaya 60S2N2A стомана. лесна структура е темперирани при гранулиран перлит. с висока пластичност. podkalivayuschayasya не при охлаждане във въздуха, след като горещо валцуване.
Пружини от аустенитна хром-никелови стомани (12X18H10T и др.), Втвърдяване чрез студено пластично деформиране. Едва след навиване се подлага на темпериране при 450 до 500 ° С се държи в продължение на 20-30 минути.
За подобряване на корозионната устойчивост и стабилност на неръждаеми стомани пролетта след всички операции на процеса се подлага на полиране (електролитна по-добре), за да завърши повърхност пояснение. Трябва да бъдат взети предвид. че за полиране с диаметър тел се намалява с 3-10%, което намалява характеристиките сила на пружините.
пружини се нагряват в хоризонтално положение. За да се избегне изкривяване по време на загряване на печка сърцето на канал железни греди. на който е поставена пружина. устройството се използва за втвърдяване на пружините на компресията. представлява стоманена чаша (вътрешен диаметър 0,3-0,4 mm по-голям от външния диаметър на пружината. 10-12 мм и височина е по-голяма от височината на пружината) с отвор на дъното. равно на средния диаметър на пролетта. Устройството се поставя на пролетта и да го зареди в пещта. След загряване до предварително определена температура и задържащо устройство с пружина изважда от пещта и се охлажда в масло (в хоризонтално положение с непрекъснато разклащане). Закалена пружина избута на устройството. кликнете върху нея от дупката в стъклото.
Изкривяване пролетта. получен чрез охлаждане. може да бъде отстранен по време на темпериране. Закалена пружина поставен върху дорник и скоба клин. В това състояние, се извършва пролет почивка. След освобождаването на изкривяването на пружината дорник. получен чрез охлаждане. елиминирани.
За да се получи необходимата твърдост и правилна форма табела извори тънки да елиминира изкривяването възникнал по време на закаляване е смекчена в дюзите на преса с електрическо загряване. Пресата има две удар - долна и горна. Вътре щампите са стоманени колела с канали. Нихром нагревателни елементи с топлоустойчива изолация, поставен в каналите на дискове. Краищата на нагревателя отстранени от матрицата на контролния панел. За топлина уплътнения резистентност са обвити с азбест изолация. Долната умират фиксиран. Горната умират с помощта на пневматичен цилиндър. управлява кран. Тя може да бъде преместен в аксиална посока. контрол на температурата се извършва чрез термодвойка. Закалена пружина се поставя върху долната матрица. горната матрица се пресова и се държи в продължение на няколко минути при температура на закаляване.
60S2 (А) се използва за производство на стомана автомобилни пружини, 50HG (А) 50HFA. 50HGFA и сътр. Spring лист се нарязва на студено. След това те удар дупки. и дръпна краищата на горещи огънати ушите. Топлинната обработка на пролетни листа. 50HGFA например стомана. извършва в съответствие със следните режими. Листовете са заредени в пещ конвейер охлаждащ газ (температура на зона I II 600-700 ° С 800-850 ° С зона III и зона 850-880 ° С). Изложение са очаквания раздел 1.2-1.5 минути 1 mm. След загряване, пружинния лист се поставя в огъване и закаляване машина. при което огъването се осъществява с охлаждане и втвърдяване на циркулиращите масло (температура на маслото 40-60 ° С). След охлаждане, пружинния лист се темперира в транспортиращ газ пещ при 550-600 ° С със закъснение от 40-45 минути. Spring лист се поставя върху конвейера на пещта до ръба. След освобождаването на пружината лист подава към резервоара за охлаждане конвейер. Бързото охлаждане с вода след темпериране предотвратява темперира крехкост. Той не се е разпаднала на потока и да подобри условията на труд в работилницата. След освобождаване на пружинния лист се подлага на изстрел взривяване. че значително увеличава тяхната граница на издръжливост. Остатъчното напрежение на натиск на външните слоеве. причинени от песъчинки взривяване. намаляване на стреса на опън във външните влакна. увеличаване на издръжливостта на пролетта листа.
По време на топлинната обработка се контролира:
а) твърдостта след закаляване (един комплект на всеки 2 работни часа) (HRC 50-60);
б) адхезия лист пружина сглобяване (на всеки два часа работа);
в) твърдостта след закаляване (HRC 40-45).
За проверка на резултатите от топлинна обработка понякога произлязат селективно подлагат на теста за издръжливост. Освен конвенционален охлаждане ефективно индукционно нагряване на пружини. изотермични втвърдяване и особено топломеханична лечение.
Втвърдяване чрез закаляване, следван от стареене.
Stuff. закаляване и стареене. на берилий бронз. Произведени от ленти (щамповане. Екстрактор. Гъвкава и т. П.), пръти (агрегати) на телта (чрез навиване) части преди да се охлади обезмаслена в ацетон или бензин. промива се със студена и кипене вода и се изсушава с топъл въздух или в сушилня при температура не по-висока от 120 ° С препарати елементи, поставени в кутията. излива въглен. се нагрява в пещ до 760-800 ° С със закъснение от 8-15 минути. охлажда в студена вода и след това се суши.
Втвърдените части са подложени на стареене (утаяване втвърдяване) при 260-400 ° С (в зависимост от желаните свойства) забавена след нагряване от 1 час до 4 часа и се охлажда на въздух. За да се избегне изкривяване на застаряването на части се извършва в специални устройства. След топлинната част. Твърдост, в зависимост от условията на експлоатация на части HV 200-400.
Охлаждане на заготовката и се подлага на последващо производство на тези части в съответствие със следния процес на производство: рязане сегмент или заготовки; обезмасляване. измиване. сушене; втвърдяване; полиране на детайли (ако е необходимо); производствени детайли; обезмасляване. промиване и сушене части. стареене; контрол.
Намери пролетта на сайта ------------------>