Материали и термична обработка - studopediya
Зъбни колела са направени от стомана. За да се осигури контакт здравина и якост на огъване на зъбите, те се подлагат на топлинна обработка. В зависимост от твърдостта на стоманени работа повърхности на зъбите се отличават: зъбни колела с твърдост по Бринел, ≤ 350 HB нормализирани, подобрени, или втвърдени и зъбно колело с твърдост> 350 НВ, закалени, случай закалени, нитрирания и tsianirovannye. Стоманени зъби с твърдост ≤ 350 N добре полирана и не претърпяват крехко разрушаване при динамични натоварвания. За най-добри разпадането зъб твърдост зъби на зъбните колела, се препоръчва да се вземат повече от твърдостта на зъбите предавка 10 - 15 единици:
Стоманени зъбни колела с твърдост ≤ 350 HB имат широко приложение в страните с ниски и средни трансмисии, както и в предавания с големи колела, които топлинна обработка е трудно.
Чрез втвърдяване - един прост метод за получаване на висока твърдост на зъбите.
Зъб става трудно през цялото време. Насипни втвърдяване изложени въглерод и легирана стомана (стомана 45, 40Х, и така 40KhN. D.). Твърдостта на повърхността на зъба 45-55 HRC (Rockwell в единици). Недостатъците на насипни охлаждане отнася увеличение измятане на зъбите и намаляване на вискозитета на сърцевината, което води до намаляване на якостта на зъбите да се огъват под действието на ударни натоварвания. Ето защо, чрез закалени в много случаи заменят с повърхностно закаляване, цементацията, азотиране и цианиране.
Повърхностно втвърдяване на високочестотни токове (HDTV) или пламък горелка осигурява 48-54 HRC и е приложим за големи зъби т ≥ 5 mm. Използва се за повърхностно закаляване на стомана 40х 40KhN, 45 и др.
Азотиране (насищане азотен повърхностен слой) осигурява висока твърдост. Малкият дебелината на твърдо вещество повърхностния слой (от около 0.1. 0.6 mm) прави зъби чувствителни към претоварване и неподходящи за използване в условия на високо износване. За azotiruemyh стоманени джанти молибден, използвани 38HMYUA или неговите заместници и 38HVFYUA 38HYUA.
Цианидиране - процесът на химико-термична обработка (стомана въглероден насищане повърхност и азот едновременно). Това увеличава механичните свойства и износоустойчивост. Цианидиране се използва за средно въглеродна стомана.
В зависимост от метода на производство на заготовки отличава гласове, ковани, пресовани колело и колелата, изработена от кръг склад. Леене на стомана е намалена сила и се използва за голям размер джанти, работещи заедно с фалшив предавка.
Чугун, използван за производството на големи, бавно движещи колела и открити зъбни колела. Основният недостатък на желязо - намалена якост на огъване. Въпреки това, желязо е изключително устойчив на умора срутването и механично увреждане влошено мазане.
Пластмасовите съоръжения са произведени основно от печатната платка и полиамиди. Основните предимства на пластмасови съоръжения в сравнение с метал включват: способността да поглъща удари, възникващи по време на променливи товари; способността да забавят механични вибрации и намаляване на предаване на шума; намалено износване на зъбите.
Допустим стрес контакт при изчисляването на умората. Изчисление на умора при циклични контактни напрежения се основава на криви умора. На фигура 11.17 крива умора е конструирана в полу-логаритмични координати: # 963; п - максималната цикъл контакт стрес; N - брой цикли; # 963; Н0 - ограничете контактите си издръжливост при otnulevom цикъл на натоварване; NN0 - база брой цикли (абсцисата на точката на умора фрактура на кривата); NH - жизнен цикъл (брой цикли на неуспех при определени контактни напрежения). Допустимо напрежение контакт определя по формулата
където SH - фактор за безопасност; KHL - съотношение издръжливост.
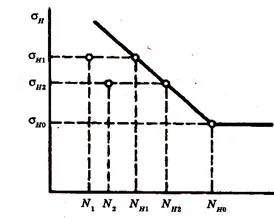
Фигура 11.17 - крива на умора при контакт циклични натоварвания
За цилиндрична и конусна предавка с малка разлика в твърдостта на предавателни зъби и колелата на базата на оценените получила две минимални допустими напрежения, определен материал за HP1 HP2 зъбни колела и колела.
фактор за безопасност - препоръчва SH> 1,1 при нормализиране или подобряване насипно охлаждане зъби (хомогенна структура по обем); SH> 1,2, с повърхностно закаляване, цементацията, азотиране (хетерогенна структура по обем).
KHL фактор трайност представлява режим на действие издръжливост и прехвърляне на товара. KHL, изготвен от крива умора (фигура 11.17). На гарата NH Експонатът за контакт стрес M = 6, а след това можем да запишем KHL фактор отчита възможността за увеличаване на допустимите напрежения за контакт за кратко работно кутия (при NHI. Изчисляване на броя на цикъла на натоварване се извършва като се има предвид начина на предаване на товара. Разграничаване режими постоянен и променлив товар. За постоянни режими на натоварване включва отклонение до 20%. За изчислява приемам товар, отговарящ на номиналната мощност на двигателя. При постоянна работа без натоварване, приблизителният брой на цикъла на натоварване в формула (11.53) където п - скорост на въртене на колелата на материала, който определя допустимото напрежение, мин -1; и - брой на зъбите на връзки на колело революция (със същия брой на колела, зацепване с броене); т - броят на часовете за предаване дизайн живот. Когато условията на променливо натоварване (вж. Циклограма на фигура 11.18) изчисление трайност фактор KHL работят на NHE еквивалентен брой цикли. Така NHE замества NHI във формула (11,53):